ஏழை கோளமயமாக்கலுக்கான 17 காரணங்கள் மற்றும் கட்டுப்பாடு
1960 கள் மற்றும் 1970 களில், கோகோவின் மோசமான தரம் (பெரிய கட்டி, குறைந்த அடர்த்தி, குறைந்த நிலையான கார்பன் உள்ளடக்கம் மற்றும் கந்தக உள்ளடக்கம்) காரணமாக குப்போலாக்கள் முக்கியமாக இரும்பு இரும்பை உற்பத்தி செய்ய பயன்படுத்தப்பட்டன; உருகிய இரும்பின் குறைந்த வெப்பநிலை; பயன்படுத்தப்படும் நொடுலைசர் தயாரித்தல் முறை சரியானது அல்ல; பன்றி இரும்பில் அதிக சல்பர் மற்றும் பாஸ்பரஸ் உள்ளடக்கம் உள்ளது, எனவே உற்பத்தி செய்யப்பட்ட முடிச்சு வார்ப்பிரும்பின் தரம் மோசமாக உள்ளது, மேலும் கோளமயமாக்கல் தரம் நிலையற்றது. இப்போதெல்லாம், முடிச்சு வார்ப்பிரும்பு உற்பத்தி பெரும்பாலும் மின்சார உலைகளில் உருக்கப்படுகிறது, மேலும் உலை வெப்பநிலையை கட்டுப்படுத்த எளிதானது; பன்றி இரும்பு போன்ற மூலப்பொருட்களின் தரம் நல்லது; பல வகையான நொதிலைசர்கள் உள்ளன மற்றும் தரம் நன்றாக உள்ளது, எனவே முடிச்சு வார்ப்பிரும்பின் தரத்தை கட்டுப்படுத்த எளிதானது. இருப்பினும், இரும்பு இரும்பு உற்பத்தியில் மோசமான கோளமயமாக்கல் இன்னும் முக்கிய குறைபாடுகளில் ஒன்றாகும்.
பெரிய கோளங்கள் அல்லது வெளிப்படையான சிறிய கருப்பு புள்ளிகளுடன், வார்ப்பு முறிவின் மீது (பொதுவாக ஊற்றும் ரைசரின் எலும்பு முறிவைக் கவனியுங்கள்) மோசமான கோளமயமாக்கல் வெளிப்படுகிறது; காஸ்டிங் அடிக்கும் ஒலி தெளிவாகவும் மிருதுவாகவும் இல்லை; மெட்டலோகிராஃபிக் மைக்ரோஸ்ட்ரக்சரில் பல தடிமனான துண்டுகள் உள்ளன; சிறிய அளவு கோள வடிவ கிராஃபைட், திரட்டப்பட்ட கிராஃபைட் அல்லது டென்ட்ரிடிக் கிராஃபைட் உள்ளன (சில நேரங்களில் மோசமான கோளமயமாக்கல் ஒரு மெட்டலோகிராஃபிக் அம்சத்தைக் கொண்டுள்ளது, அதாவது தடிமனான ஃப்ளேக் கிராஃபைட் கிளஸ்டர்களில், தனிப்பட்ட கோள வடிவ கிராஃபைட்டுகள் வட்டமானவை) .
ஏழை கோளமயமாக்கலுக்கான காரணங்கள் பொதுவாக பின்வரும் மூன்று வகையான காரணிகளால் பாதிக்கப்படுகின்றன: மீதமுள்ள மெக்னீசியம் உள்ளடக்கம் அல்லது அரிய பூமி உள்ளடக்கம் மிகக் குறைவாக உள்ளது (ஆனால் அரிதான பூமியின் உள்ளடக்கம் மிக அதிகமாக இருக்கும்போது, கிராஃபைட் வட்டமானது மோசமாகிறது, மற்றும் வார்ப்பு வாய்ப்புள்ளது வெள்ளை வாய்க்கு. மற்றும் சுருங்கும் பைன்); தடுப்பூசி விளைவு வலுவாகவோ அல்லது குறையவோ இல்லை; குறுக்கீடு உறுப்பு மிக அதிகமாக உள்ளது.
இருப்பினும், உண்மையான உற்பத்திச் செயல்பாட்டில், தொழில்நுட்பக் கோளாறுகள், செயல்பாட்டுச் சிக்கல்கள் மற்றும் மேலாண்மைச் சிக்கல்கள் உள்ளிட்ட மோசமான கோளமயமாக்கலை ஏற்படுத்தும் பல காரணிகள் உள்ளன.
1. ஸ்பீராய்டிங் முகவரின் மோசமான தரம்
ஸ்பீராய்டிங் ஏஜெண்டில் Mg மற்றும் RE இன் உள்ளடக்கம் ஆய்வக சோதனைகள் மூலம் தரத் தேவைகளைப் பூர்த்தி செய்தாலும், MgO உள்ளடக்கம் ஒப்பீட்டளவில் உயர்வானது. MgO மேம்படுத்தலாம் கோளமயமாக்கலின் தரமானது கிட்டத்தட்ட எந்த விளைவையும் ஏற்படுத்தாது, ஆனால் இரும்பு இரும்பு கசடு சேர்க்கும் குறைபாடுகளுக்கு ஆளாகிறது; ஸ்பீராய்டிங் முகவர் Ca போன்ற குறைவான கூறுகளைக் கொண்டுள்ளது, ஸ்பீராய்டிங் சிகிச்சையின் போது எதிர்வினை தீவிரமானது, மேலும் Mg அதிகமாக எரிகிறது.
தடுப்பு நடவடிக்கைகள்: மோசமான தரமான நொடுலைசர்களைப் பயன்படுத்த வேண்டாம் (சப்ளையர்கள் மற்றும் உற்பத்தியாளர்களை பரிசோதிக்க வேண்டும், முதலில் சிறிய அளவில் வாங்கவும், பின்னர் சோதனைக்கு பிறகு மொத்தமாக வாங்கவும்). கோளமயமாக்கல் முகவர் நீண்ட நேரம் வைக்கப்படுகிறது, மேலும் அது ஈரமாக மற்றும் ஆக்ஸிஜனேற்றப்படுவது எளிது.
2. உலை முன் கோளமயமாக்கலின் தவறான செயல்பாடு
உருகிய இரும்பு லேடில் அணையின் குழிக்குள் கோளமயமாக்கல் முகவர் ஊற்றப்படுகிறது, அது தட்டையாக இல்லை; மேற்பரப்பு மூடுதல் சிறியது, அல்லது மூடுதல் அடுக்கு மெல்லியதாக இருக்கும் அல்லது ஸ்பீராய்டிங் ஏஜென்ட் தொகுதியின் இடைவெளி நிரப்பப்படவில்லை. உருகிய இரும்புக்குள் விரைந்த பிறகு, கோளமயமாக்கல் வெளிப்படுவது மட்டுமல்லாமல் முகவர் உடனடியாக உருகி வினைபுரிகிறது, அதே நேரத்தில், உருகிய இரும்பு ஒரு பெரிய அளவு கோளமயமாக்கல் முகவர் தொகுதியின் இடைவெளியில் நுழைகிறது, நேரடியாக கோளமயமாக்கல் முகவரை உருக்குகிறது அல்லது கோளத்தை கழுவுகிறது மிதக்கும் உருகிய இரும்பின் மேற்பரப்பில் உள்ள முகவர், எதிர்வினை மிக விரைவாகவும் வேகமாகவும் இருக்கும், மேலும் Mg அதிகமாக எரிகிறது.
தடுப்பு நடவடிக்கைகள்: பையின் அடிப்பகுதியில் உள்ள குழிக்குள் ஊற்றப்பட்ட ஸ்பீராய்டிங் ஏஜெண்டை தட்டவும், சரியான முறையில் அடிக்கவும், பின்னர் அதன் மீது மூடப்பட்ட தடுப்பூசி போடப்பட்ட ஃபெரோசிலிக்கானை தட்டவும் மற்றும் அடிக்கவும், மற்றும் பொருத்தமான அளவு முடிச்சு வார்ப்பிரும்பு தாக்கல் (பவுண்டட்) அல்லது டக்டைல் இரும்பு குறிப்பிட்ட தடிமன் கொண்ட தட்டு. இது உலோகக்கலவையின் இடைவெளிகளை நிரப்புவது மட்டுமல்லாமல், ஒரு குறிப்பிட்ட தடிமன் கொண்ட அடுக்கையும் கொண்டுள்ளது.
3. அசல் உருகிய இரும்பில் அதிக சல்பர் உள்ளடக்கம் உள்ளது
சல்பர் முக்கிய டி-ஸ்பீராய்டிங் உறுப்பு ஆகும், மேலும் அதிக கந்தக உள்ளடக்கம் கோளமயமாக்கலின் தரத்தை கடுமையாக பாதிக்கும். அசல் உருகிய இரும்பில் உள்ள WS 0.06%ஐ விட அதிகமாக இருக்கும்போது, அதிக ஸ்பீராய்டிங் முகவர் சேர்க்கப்பட்டாலும் தகுதியான முடிச்சு வார்ப்பிரும்பு தரத்தைப் பெறுவது கடினம். . ஸ்பீராய்டிசிங் செயல்பாட்டின் போது, உருளை இரும்பில் உள்ள எம் உடன் முதன்முதலில் உருகிய இரும்பில் உள்ள வேதியியல் ரீதியாக வினைபுரிந்து எம்ஜிஎஸ் ஒரு கசடு உருவாகிறது, மீதமுள்ள எம்ஜி கோளமயமாக்கலின் பாத்திரத்தை வகிக்கிறது, இது RE க்கும் பொருந்தும். சில ஸ்பீராய்டிசிங் கூறுகள் இருப்பதால், கோளமயமாக்கலின் தரம் பாதிக்கப்படுகிறது. உருகிய இரும்பில் அதிக சல்பர் உள்ளடக்கம் உள்ளது. அதிக அளவு ஸ்பீராய்டிங் ஏஜெண்ட் சேர்க்கப்பட்டாலும், கொட்டும் நேரம் மிக நீளமாக இருந்தால் மற்றும் கசடு சுத்தமாக இல்லாவிட்டால், "ரிட்டர்ன் சல்பர்" என்ற நிகழ்வு ஏற்படும், இது ஊற்றுவதில் இருந்து பிந்தைய நிலை வரை வார்ப்புகளின் தரத்தை பாதிக்கும். . அசல் உருகிய இரும்பில் கந்தகத்தின் முக்கிய ஆதாரம்: அதிக கந்தக உள்ளடக்கம் கொண்ட கோக் அல்லது புதிய இரும்பு பயன்பாடு.
தடுப்பு நடவடிக்கைகள்: குறைந்த சல்பர் பன்றி இரும்பு மற்றும் மறுசுழற்சி பொருள் மற்றும் கோக் பயன்படுத்தவும்; சேர்க்கப்பட்ட நொதிலைசரின் அளவுக்கும் அசல் உருகிய இரும்பின் கந்தக உள்ளடக்கத்திற்கும் இடையிலான உறவைப் புரிந்து கொள்ளுங்கள்; உலைக்கு முன்னால் மற்றும் கோளமயமாக்கல் செயல்பாட்டின் போது (கோக் மீது சுண்ணாம்பு தெளிக்கவும்) நீரிழப்பு நடவடிக்கைகளை எடுக்கவும், நீர் மற்றும் மின்சார உலைகளால் கந்தகமாக்குவது எளிது, கோள மேற்பரப்பு அல்லது காஸ்டிக் சோடாவை ஸ்பீராய்டிங் பையில் சேர்க்கவும்)
டி, எஸ்பி, ஆஸ், பிபி, ஆல், எஸ்என், போன்ற சார்ஜுடன் மாற்றியமைக்கப்பட்ட ஸ்பீராய்டிசேஷன் குறுக்கீடு கூறுகள் மிக அதிகமாக உள்ளன உருகிய இரும்பில் இன்னும் கிராஃபைட் முடிச்சுகளின் வடிவம் சிதைந்துவிடும் (சிதைந்த கிராஃபைட்); கோளமயமாக்கல் இருந்தாலும், முடிச்சு வார்ப்பிரும்பு பொருட்களின் இயற்பியல் பண்புகளும் மிகவும் உடையக்கூடியதாக இருக்கும். எனவே, QT400-18 மற்றும் குறைந்த வெப்பநிலை எதிர்ப்பு டக்டைல் இரும்பு உற்பத்தியில், அதிக தூய்மையான பன்றி இரும்பு பயன்படுத்தப்பட வேண்டும்.
4. உருகிய இரும்பு லேடலின் முறையற்ற இடம்
இரும்பைத் தட்டும்போது, உருகிய இரும்பு நேரடியாக குழியில் அழுத்தும் கோளமயமாக்கல் முகவருக்கு விரைகிறது, இது மூடியைக் கழுவுவது மட்டுமல்லாமல், அதிக வெப்பநிலை உருகிய இரும்பின் தாக்கத்திற்கு நேரடியாக கலவைத் தொகுதியை உருவாக்குகிறது, அல்லது முன்கூட்டியே உருகும், வன்முறையில் வினைபுரிகிறது, அல்லது இரும்புக்கு விரைவாக மிதக்கிறது உருகிய இரும்பின் மேற்பரப்பு உருகிய இரும்பின் மேற்பரப்பில் உருகி எரிகிறது மற்றும் காற்றால் உறிஞ்சப்படுகிறது, இது உருகிய இரும்பின் உறிஞ்சுதல் வீதத்தை Mg ஆக குறைக்கிறது.
தடுப்பு நடவடிக்கைகள்: உருகிய இரும்பு கலவை நேரடியாக கலவை பாதிக்காமல் இருக்க உருகிய இரும்பு லேடலை வைக்கவும், இதனால் உருகிய இரும்பு அலாய் சீராகவும் விரைவாகவும் மூழ்கி ஒரு குறிப்பிட்ட ஆழத்தை உடனடியாக அடையலாம், மேலும் அலாய் மிதக்கும் தூரத்தை அலாய் நீட்டவும் உருகிய இரும்பினால் முழுமையாக உறிஞ்சப்படலாம்.
5. மெதுவாக இரும்பு தட்டுதல் தொடங்குகிறது
ஆரம்பத்தில் இரும்புத் தட்டுதல் மிகவும் மெதுவாக இருந்தால், திரவ நிலை லேடில் மெதுவாக உயரும். உருகிய இரும்பு அலாய் வெள்ளம் வரும்போது, உலோகக்கலவையின் மேற்பரப்பு அடுக்கு உருகி பின்னர் உயரத் தொடங்கும். உலோகக்கலவையின் மேற்பரப்புக்கும் உருகிய இரும்பின் மேற்பரப்புக்கும் இடையே உள்ள குறுகிய தூரம் காரணமாக, உலோகக்கலவைக்கு நேரமில்லை உருகிய இரும்பின் மேற்பரப்பில் அதிக அளவு உருகிய இரும்பு மிதக்கிறது. உருகிய இரும்பின் மேற்பரப்பில் உருகும் மற்றும் எரியும் காற்றினால் உறிஞ்சப்பட்டு இழக்கப்படுகிறது, இது உருகிய இரும்பின் உறிஞ்சுதல் வீதத்தை Mg ஆக குறைக்கிறது.
தடுப்பு நடவடிக்கைகள்: குபோலா உலைகளுக்கு, முன் அடுப்பில் போதுமான உருகிய இரும்பு இருக்க வேண்டும். தட்டுவதற்கு முன், குழாய் குழியைத் தடுக்கும் சேற்றை அகற்றி, உருகிய இரும்பை விரைவாகச் சென்றடைய விரைவாக குழாய் திறக்கவும். உருகிய இரும்பு லேடில் திறனின் ஆழத்தின் 2/3 (அதாவது ஒரு குறிப்பிட்ட ஆழம்). இந்த நேரத்தில், கலப்பு மேற்பரப்பில் இருந்து திரவ மேற்பரப்பிற்கு பெரிய தூரம் காரணமாக கோளமயமாக்கல் எதிர்வினை ஏற்படுகிறது. உருகிய இரும்பில் அலாய் மிதக்கும் போது, அது பயணிக்கும் தூரம் நீண்டது, மற்றும் அலாய் ஒரே நேரத்தில் மிதந்து உருகும். , விளிம்பு உருகிய இரும்பினால் முழுமையாக உறிஞ்சப்படுகிறது, ஸ்பீராய்டிங் ஏஜெண்டில் Mg என்ற ஸ்பீராய்டிங் உறுப்பு அதிக உறிஞ்சுதல் வீதத்தைக் கொண்டுள்ளது, மேலும் முடிச்சு வார்ப்பிரும்பின் தரம் நன்றாக உள்ளது. மின்சார உலை தட்டுதல் மிகவும் வசதியானது, விரைவாகத் தட்டத் தொடங்குங்கள், மெதுவாகத் தட்டுதல் அல்லது எதிர்வினை வன்முறையில் இருக்கும்போது தட்டுவதை நிறுத்துதல், மற்றும் எதிர்வினை நிலையானதாக இருக்கும்போது தேவையான அளவு தட்டுவதைத் தொடரவும். பதில் நிலையானதாக இருந்தால், முடிந்தவரை வேகமாகவும் பின்னர் மெதுவாகவும் முயற்சி செய்யுங்கள் (நடுவில் இடைவிடாமல்) ஒரு முறை.
6. கோளமயமாக்கல் முகவர் மிக விரைவாக நிறுவப்பட்டது அல்லது அணையின் குழியில் உருகிய இரும்பு முழுமையாக ஊற்றப்படவில்லை
ஊற்றிய பிறகு, சிவப்பு சூடான லேடலின் அடிப்பகுதியில் வெப்பநிலை 900 ° C ஐ விட அதிகமாக உள்ளது. ஸ்பீராய்டிங் முகவர் உடனடியாக நிறுவப்பட்டால், Mg மற்றும் RE இன் ஒரு பகுதி அதிக வெப்பநிலை பேக்கிங் (புகை நிகழ்வு) கீழ் இழக்கப்படும்; பள்ளத்தில் உருகிய இரும்பை சுத்தம் செய்யாவிட்டால், Mg இழப்பு அதிகமாக இருக்கும்; கூடுதலாக, அதிக வெப்பமடையும் முன் வெப்பமூட்டும் வெப்பநிலை ஸ்பீராய்டிங் முகவரின் முன்கூட்டிய உருகலை ஊக்குவிக்கும்.
தடுப்பு நடவடிக்கைகள்: லாடலை சிறிது நேரம் குளிர்விக்க விடுங்கள், உருகிய இரும்பைத் தட்டுவதற்கு முன் கோளமயமாக்கல் முகவரை நிரப்பவும். அதே சமயத்தில், ஊற்றிய பிறகு மீதமுள்ள உருகிய இரும்பை லேடலில் ஊற்றி, உருகிய கசடுகளை அகற்றவும்.
7. உருகிய இரும்பின் உருளைகளின் வெப்பநிலை மிகவும் குறைவாக உள்ளது
உருகிய இரும்பு வெப்பநிலை 1390 டிகிரிக்கு குறைவாக இருக்கும்போது, அலாய் உருகுவது எளிதல்ல, கோளமயமாக்கல் எதிர்வினை முழுமையடையாது, மற்றும் கோளமயமாக்கல் நிலை தேவைகளைப் பூர்த்தி செய்வது கடினம். உருகிய இரும்பின் குறைந்த வெப்பநிலை காரணமாக, ஸ்பீராய்டிங் ஏஜெண்டின் மிதக்கும் செயல்பாட்டின் போது, ஸ்பீராய்டிங் முகவர் உருகிய இரும்பின் மேற்பரப்பில் மிதந்து, உருகிய இரும்பின் மேற்பரப்பில் மிதக்க காரணமாக உருகும் இரும்பின் உருகலை விரைவாக உறிஞ்ச முடியாது.
8. உருகிய இரும்பின் உருளைகளின் வெப்பநிலை மிக அதிகம்
ஸ்பீராய்டிங் திரவ இரும்பின் வெப்பநிலை மிக அதிகமாக உள்ளது, மேலும் மூடும் முகவர் மற்றும் கோளமயமாக்கல் முகவரின் உருகும் வேகம் மிக வேகமாக உள்ளது. தூய Mg இன் அடர்த்தி 1.74g/cm3 என்பதால், உருகும் இடம் 651 ° C, மற்றும் கொதிநிலை 1105 ° C ஆகும். உருகும் புள்ளி, ஆனால் 1400 than க்கும் குறைவாக, கோளமயமாக்கல் வெப்பநிலை பெரும்பாலும் 1490 ~ 1520 is என்று குறிப்பிடவில்லை, மேலும் சில அதிகமாக இருக்கலாம். வார்ப்பின் அளவு மற்றும் வார்ப்பு சுவரின் தடிமன் ஆகியவற்றின் படி, கோளமயமாக்கல் வெப்பநிலையை உண்மையில் அதிகரிக்க வேண்டியிருக்கும் போது, ஒப்பீட்டளவில் "குறைந்த வெப்பநிலை சிகிச்சை மற்றும் அதிக வெப்பநிலை வார்ப்பு" நடவடிக்கைகள் எடுக்கப்பட வேண்டும். கூடுதலாக, உருகிய இரும்பின் வெப்பநிலை மிக அதிகமாக இருந்தால், உருகிய இரும்பு பெரும்பாலும் தீவிரமாக ஆக்ஸிஜனேற்றப்படுகிறது. Mg மற்றும் RE ஆக்சைடுகளுடன் எளிதில் வினைபுரிவதால், அதிக வெப்பநிலை அதிக அளவு இழப்பு மற்றும் Mg மற்றும் RE ஆவியாதலை ஏற்படுத்துகிறது, இது உறிஞ்சுதல் வீதத்தை குறைக்கிறது.
9. கோளமயமாக்கல் முகவர் சிறிய கட்டிகள் மற்றும் அதிக உடைந்த துண்டுகளைக் கொண்டுள்ளது
ஸ்பீராய்டிங் ஏஜெண்டின் அளவு சிறியதாக இருக்கும் போது மற்றும் பல துண்டுகள் இருக்கும் போது, ஸ்பீராய்டிங் சிகிச்சை முறை ஒன்றே என்றாலும், அலாய் தொகுதிகளுக்கு இடையில் இடைவெளிகள் இல்லாததால், உருகும் எதிர்வினை மெதுவாக உரிக்கப்பட்டு அடுக்கு அடுக்காக மட்டுமே இருக்கும். ஊற்றுவதற்கு அதே படிகள் பயன்படுத்தப்பட்டால், முதல் சில பெட்டிகளின் கோளமயமாக்கல் நன்றாக இல்லை மற்றும் கடைசி சில பெட்டிகளின் கோளமயமாக்கல் இன்னும் நன்றாக இருக்கும்.
தடுப்பு நடவடிக்கைகள்: உருகிய இரும்பு லேடலின் அளவை அடிப்படையாகக் கொண்ட ஸ்பீராய்டிங் ஏஜெண்டின் அளவைத் தேர்ந்தெடுக்கவும், அதாவது எவ்வளவு உருகிய இரும்பு கோளமாக உள்ளது. அதிகமாக நசுக்கியிருந்தால், அதை சல்லடை செய்ய வேண்டும்; கோளமயமாக்கல் எதிர்வினை மிகவும் மெதுவாக இருந்தால், உருகிய இரும்பின் மூலம் ஏற்றப்பட்ட உலோகக்கலவையை சில முறை நொறுக்க ஒரு எஃகு துரப்பணம் பயன்படுத்தப்படலாம், மேலும் உருகிய இரும்பை கலப்புக்குள் துளையிடலாம்.
10. கோளமயமாக்கல் முகவர் மிகப் பெரியது
கோளமயமாக்கல் முகவர் மிகப் பெரியது. மிதக்கும் மற்றும் உருகும் செயல்பாட்டின் போது, அது உருகிய இரும்பினால் சரியான நேரத்தில் உறிஞ்சப்படுவதில்லை, ஆனால் உருகிய இரும்பின் மேற்பரப்பில் உருகுவதற்கும் எரிப்பதற்கும் மிதந்து, காற்றில் வீணாகிறது.
உருகிய இரும்பு லேடலின் அளவைப் பொறுத்து, உருகிய இரும்பின் முடிச்சியின் அளவைப் பொறுத்து, ஸ்பீராய்டிங் முகவர் தொகுதி அளவின் தேர்வு தீர்மானிக்கப்படுகிறது.
11. சிறிய அளவு ஸ்பீராய்டிங் முகவர் சேர்க்கப்பட்டது
சேர்க்கப்பட்ட ஸ்பீராய்டிங் ஏஜென்ட்டின் அளவு பொருளின் தேவைகள், உருகிய இரும்பின் சல்பர் உள்ளடக்கம், உருகிய இரும்பின் தரம், கோளமயமாக்கல் வெப்பநிலை, வார்ப்பின் அளவு மற்றும் பிற காரணிகளுடன் தொடர்புடையது. சிறிய அளவு கோளமயமாக்கல் முகவர் இரண்டு காரணங்கள் உள்ளன: ஒன்று வடிவமைப்பு தேவை தானே சிறியது; மற்றொன்று, உருகிய இரும்பின் அளவு நன்கு கட்டுப்படுத்தப்படவில்லை, மேலும் உருகிய இரும்பின் அளவு தேவையை மீறுகிறது.
12. இரும்பு திரவ ஆக்சிஜனேற்றம்
ஆக்ஸிஜனேற்றத்திற்குப் பிறகு உருகிய இரும்பின் ஆக்ஸிஜன் உள்ளடக்கம் அதிகமாக உள்ளது. O மற்றும் Mg க்கு இடையேயான வலுவான தொடர்பு காரணமாக, ஸ்பீராய்டிங் ஏஜெண்டில் உள்ள Mg என்ற பயனுள்ள ஸ்பீராய்டிங் உறுப்பு முதலில் O உடன் இணைந்து MgO கசடு தயாரிக்கப்படுகிறது, மீதமுள்ள Mg கிராஃபைட்டை உருட்டலாம். செயல்பாடு, ஏனென்றால் ஆக்ஸிஜன் அதிக அளவு Mg ஐப் பயன்படுத்துகிறது, மீதமுள்ள Mg கிராஃபைட் கோளமானது என்பதை உறுதிப்படுத்த போதுமானதாக இல்லை, எனவே கோளமயமாக்கல் நிலை குறைவாக உள்ளது மற்றும் கோளமயமாக்கல் தரம் மோசமாக உள்ளது.
தடுப்பு நடவடிக்கைகள்: உருகிய இரும்பு ஆக்ஸிஜனேற்றப்படுவதைத் தடுக்க குபோலாவின் குறைந்த கோக் (கரி) உயரத்திற்கு கவனம் செலுத்துங்கள்; மின்சார உலை உருகுவது, உருகிய இரும்பின் அதிக வெப்பநிலை அல்லது அதிக வெப்பம் மற்றும் நீண்ட கால வெப்பப் பாதுகாப்பைத் தடுக்க அதிகப்படியான ஆக்ஸிஜனேற்றப்பட்ட கட்டணத்தைப் பயன்படுத்த வேண்டாம், குறிப்பாக 10t உலை உருகிய இரும்பை உருகுவதற்கு. ஒவ்வொரு முறையும் ஸ்பீராய்டிசிங் செயல்முறை 1t ஆகும், ஸ்பெராய்டிங் செயல்முறை சில பொதிகளுக்குப் பிறகு, உலைகளில் உருகிய இரும்பு நீண்ட காலம் தங்கியிருப்பதால், உருகிய இரும்புக்கு "படிக கருக்கள்" இல்லை, ஆனால் ஆக்ஸிஜனேற்ற எளிதானது. கோளமயமாக்கல் செயல்முறைக்குப் பிறகு ஒரு சில பாக்கெட்டுகள், முதலில் உலையில் "முன்கூட்டிய சிகிச்சையை" மேற்கொள்ளும் போது, தகுந்த அளவு சிலிக்கான் கார்பைடு, டீஆக்ஸைடைசர், ரீகார்பூரைசர், ஃபெரோசிலிகான், முதலியவற்றை டீஆக்ஸிடேஷன் சிகிச்சைக்காகச் சேர்க்கவும், மேலும் அதிக ஸ்பீராய்டிங் முகவரைச் சேர்க்கவும்.
13. பை மற்றும் பை குழியின் ஆழம் முதல் விட்டம் வரை விகிதம்
- (1) ஸ்பீராய்டிசேஷன் தொகுப்பின் ஆழம் H இன் நேரடி D க்கு விகிதம்: H/D = 1.5 ~ 2. அரை பையை சமாளிக்க ஸ்பீராய்டிங் பை பயன்படுத்தப்பட்டால், அது உயர் பொருளாதார விகிதத்தின் அசல் நோக்கத்திற்கு எதிராக செல்கிறது.
- (2) ஸ்பெராய்டிங் ஏஜென்ட் மற்றும் கவரிங் ஏஜெண்ட்டை நிரப்பிய பின் ஸ்பீராய்டிங் பையின் குழியின் ஆழம் 20 ~ 30 மிமீ இருக்க வேண்டும். உருகிய இரும்பு குழிக்குள் நுழைகிறது மற்றும் மூடி முகவர் அரை திடமான பொருளாக உருகும், இது கோளமயமாக்கல் முகவர் முன்கூட்டியே வெடிப்பதை தாமதப்படுத்துகிறது. எம்ஜி விளைச்சலை மேம்படுத்த முடியும்.
- (3) பையின் அடிப்பகுதியில் உள்ள குழியின் அகலம் பையின் அடிப்பகுதியின் விட்டம் 1/4 முதல் 1/3 வரை இருக்க வேண்டும். திட்டமிடப்பட்ட சிறிய பகுதியைக் கொண்ட குழி ஆழத்தை அதிகரிக்கிறது மற்றும் வெடிப்பை தாமதப்படுத்த உதவுகிறது.
- (4) ஊற்றிய பின் சரியான நேரத்தில் பையில் உள்ள ஸ்லாக்ஸை சுத்தம் செய்யுங்கள், இதனால் ஒவ்வொரு கோள உருண்டை ஏஜென்டும் அதே வழியில் குழிக்குள் ஏற்றப்படும்.
14. நீண்ட நேரம் ஊற்றும் நேரம் மற்றும் பிற காரணங்களால் ஸ்பீராய்டிசேஷன் குறைகிறது
கோளமயமாக்கல் மந்தநிலையின் பண்புகள்: உலைக்கு முன்னால் நல்ல கோளமயமாக்கல் ஆனால் வார்ப்பில் நல்ல கோளமயமாக்கல் இல்லை; அல்லது உருகிய இரும்பின் அதே லேடில், முதலில் ஊற்றப்படும் வார்ப்புகளுக்கு நல்ல கோளமயமாக்கல் உள்ளது, பின்னர் ஊற்றப்படும் வார்ப்புகள் நன்றாக கோளமாக்கப்படவில்லை. அதிக நேரம் ஊற்றுவதால் ஏற்படும் கோளமயமாக்கல் மந்தநிலை பெரும்பாலும் கர்ப்பகால மந்தநிலையுடன் சேர்ந்துள்ளது. கிராஃபைட் கோளமயமாக்கப்படுவதை உறுதி செய்யும் எஞ்சிய Mg இன் அளவு உருகிய இரும்பின் கோளமயமாக்கல் தரத்தை தீர்மானிக்கிறது. Mg க்கு O மற்றும் S. Mg உடன் ஒரு வலுவான தொடர்பு உள்ளது MgO ஐ உருவாக்கி அதை எரிக்க. குறிப்பாக எஸ், எஸ் எம்ஜி உடன் இணைந்து எம்ஜிஎஸ் ஸ்லாக் தயாரிக்கும்போது, அது திரவ மேற்பரப்பில் மிதக்கிறது. திரவ மேற்பரப்பில் மிதந்த பிறகு, MgS ஸ்லாக்கில் உள்ள Mg காற்றில் O உடன் இணைந்து MgO ஐ உருவாக்கி எரிக்கிறது, மேலும் பிரிக்கப்பட்ட S அது மீண்டும் உருகிய இரும்புக்குத் திரும்பி Mg உடன் இணைகிறது. உருகிய இரும்பில் உள்ள S ஒரு படகு போன்றது, தொடர்ந்து உருகிய இரும்பில் உள்ள Mg ஐ காற்றில் கொண்டு வந்து எரிக்கிறது, இது "தலைகீழ் நிகழ்வு" என்று அழைக்கப்படுகிறது. கொட்டும் நேரத்தின் நீளத்துடன், உருகிய இரும்பில் எஞ்சியின் எஞ்சிய அளவு குறைவாகவும் குறைவாகவும் மாறும். சில தகவல்களின்படி, ஊற்றும் நேரத்தின் நீட்டிப்புடன், உருகிய இரும்பில் Mg இன் எரியும் இழப்பு ஒவ்வொரு 0.004 நிமிடத்திற்கும் 1% ஆகும்.
தீர்வு: கொட்டும் நேரம் சில காரணங்களால் நீடிக்கப்பட்டால், உருகிய இரும்பு மற்றும் காற்றுக்கு இடையேயான தொடர்பைக் குறைப்பதற்கும், உருகிய இரும்பில் எரிக்கப்பட்ட எமியின் அளவைக் குறைப்பதற்கும் பொருத்தமான இன்சுலேடிங் ஏஜென்ட்டின் தடிமன் மூடப்பட்டிருக்கும். கூடுதலாக, வளர்ந்த மற்றும் சிதைந்த கிராஃபைட்டை சிதைக்க அல்லது துண்டிக்க பொருத்தமான பின்தொடர்தல் தடுப்பூசி நடவடிக்கைகள் எடுக்கப்பட வேண்டும் (அது வளரும் போது ஃப்ளேக் கிராஃபைட் ஆகிறது) அதனால் அதன் வடிவம் கோளமாக இருக்கும்.
15. இனப்பெருக்க மந்தநிலை
மெட்டலோகிராஃபிக் பகுப்பாய்வின் மூலம், அடைகாக்கும் வீழ்ச்சியின் மெட்டலோகிராஃபிக் புகைப்படங்களில், கிராஃபைட் பந்துகளின் எண்ணிக்கை சிறியது, பந்து விட்டம் பெரியது, அடர்த்தி மெல்லியது மற்றும் கோளமயமாக்கல் நிலை குறைவாக இருப்பதைக் காணலாம். பொதுவாக, ஃபெரைட்டின் உள்ளடக்கம் குறைவாக உள்ளது, பெர்லைட்டின் உள்ளடக்கம் அதிகரிக்கிறது, மற்றும் கார்பைடுகள் உள்ளன. உள்ளன தடுப்பூசி சரிவுக்கான காரணம், தடுப்பூசி சிறிய அளவில் சேர்க்கப்படுவது அல்லது தடுப்பூசி செயல்முறை சரியாக இல்லை. ஏனெனில் மெக்னீசியம் இருப்பது கோளமயமாக்கலுக்கு அவசியமான நிபந்தனையாகும், மேலும் தடுப்பூசியில் உள்ள கூறுகள் கிராஃபிடைசேஷனில் பங்கேற்பதற்கு போதுமான நிபந்தனைகளாகும், எனவே கோளமயமாக்கல் சிகிச்சை மட்டுமே வலியுறுத்தப்படவில்லை, மேலும் உயர்தர டக்டைல் இரும்பு தயாரிக்க இயலாது.
தடுப்பு நடவடிக்கைகள்: சேர்க்கப்பட்ட தடுப்பூசியின் அளவை அதிகரிக்கவும்; பேரியம் மற்றும் கால்சியம் கொண்ட நீண்ட செயல்பாட்டு தடுப்பூசிகளைப் பயன்படுத்துங்கள்; இரண்டாம் நிலை தடுப்பூசி, மிதக்கும் சிலிக்கான் தடுப்பூசி மற்றும் ஓட்டம் தடுப்பூசி உள்ளிட்ட கூட்டு தடுப்பூசி நடவடிக்கைகளை எடுக்கவும்.
16. ஸ்பீராய்டிங் பை அல்லது ஊற்றும் பை ஈரமாக உள்ளது
உருகிய இரும்பில் ஸ்பீராய்டிங் செயல்முறை பறிமாறும்போது, நீர் ஆவியாகி சிதைந்து ஹைட்ரஜன் மற்றும் ஆக்ஸிஜனை உற்பத்தி செய்கிறது. ஓ ஸ்பீராய்டிங் ஏஜெண்டில் Mg இன் ஒரு பகுதியை நடுநிலையாக்கி MgO ஸ்லாக் ஆகிவிடும், இது உருகிய இரும்பில் உள்ள மெக்னீசியம் உள்ளடக்கத்தை குறைப்பது மட்டுமல்லாமல், வார்ப்புகளில் கசடு துளைகள் மற்றும் துளை குறைபாடுகளை உருவாக்குவது எளிது.
17. ஆன்-சைட் மேலாண்மை
கோளமயமாக்கல் முகவரின் மேலாண்மை மற்றும் ஸ்டாக்கிங் தரப்படுத்தப்படவில்லை, மேலும் ஃபெரோசிலிகான் கலக்கப்படலாம்; ஸ்பீராய்டிங் ஏஜெண்டின் எடை துல்லியமற்றது, அல்லது உரித்தல் அல்லது தவறாகப் படித்தல் போன்றவை இல்லை. உதாரணமாக, ஒரு குறிப்பிட்ட தொழிற்சாலையில் டக்டைல் வார்ப்பிரும்பின் உற்பத்தித் தரம் மிகவும் நிலையானது. திடீரென்று, இரண்டு உலைகளும் இரவு நேரத்திற்கு முன் மோசமான கோளமயமாக்கலைக் கொண்டிருந்தன, மேலும் ஆய்வக பகுப்பாய்வில் சிலிக்கான் உள்ளடக்கம் தரத்தை மீறியது. ஆராய்ச்சி மற்றும் பகுப்பாய்விற்குப் பிறகு, தரையில் சிதறியிருக்கும் ஃபெரோசிலிகான் பகலில் சுத்தம் செய்யப்பட்டிருக்கலாம். , Spheroidizing முகவர் தொட்டியில் வரிசைப்படுத்தப்பட்டது. கூடுதலாக, கோளமயமாக்கல் முகவரின் சேமிப்பு நேரம் மிக நீண்டது மற்றும் சேமிப்பு நன்றாக இல்லை. ஸ்பீராய்டிங் ஏஜெண்டின் ஆக்சிஜனேற்றம் கோளமயமாக்கல் விளைவை வலுவிழக்கச் செய்து, ஸ்பீராய்டிசின் தரத்தை பாதிக்கும்.
இறுதியான குறிப்புகள்
தினசரி வேலைகளில், கடினமாக உழைக்க மற்றும் உழைக்காமல் இருக்க தேவையான கடின உழைப்பும் முயற்சியும் ஒத்ததாக இருக்கிறது, ஆனால் தயாரிப்பு தரத்தை மேம்படுத்துவதிலும் நிலைப்படுத்துவதிலும் மற்றும் ஆபரேட்டர்களின் தொழில்நுட்ப அளவை மேம்படுத்துவதிலும் பெரிய வித்தியாசம் உள்ளது.
மறுபதிப்புக்கு இந்த கட்டுரையின் மூலத்தையும் முகவரியையும் வைத்திருங்கள்: ஏழை கோளமயமாக்கலுக்கான 17 காரணங்கள் மற்றும் கட்டுப்பாடு
மிங்கே டை காஸ்டிங் கம்பெனி தரமான மற்றும் உயர் செயல்திறன் கொண்ட வார்ப்பு பாகங்கள் (மெட்டல் டை காஸ்டிங் பாகங்கள் வரம்பில் முக்கியமாக அடங்கும் மெல்லிய-வால் டை காஸ்டிங்,ஹாட் சேம்பர் டை காஸ்டிங்,கோல்ட் சேம்பர் டை காஸ்டிங்), சுற்று சேவை (டை காஸ்டிங் சேவை,சி.என்.சி எந்திரம்,அச்சு தயாரித்தல், மேற்பரப்பு சிகிச்சை) .ஒரு விருப்ப அலுமினிய டை காஸ்டிங், மெக்னீசியம் அல்லது ஜமாக் / துத்தநாக டை வார்ப்பு மற்றும் பிற வார்ப்பு தேவைகள் எங்களை தொடர்பு கொள்ள வரவேற்கப்படுகின்றன.
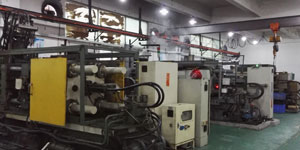
ISO9001 மற்றும் TS 16949 ஆகியவற்றின் கட்டுப்பாட்டின் கீழ், அனைத்து செயல்முறைகளும் நூற்றுக்கணக்கான மேம்பட்ட டை காஸ்டிங் இயந்திரங்கள், 5-அச்சு இயந்திரங்கள் மற்றும் பிற வசதிகள் மூலம் மேற்கொள்ளப்படுகின்றன, அவை பிளாஸ்டர்கள் முதல் அல்ட்ரா சோனிக் சலவை இயந்திரங்கள் வரை உள்ளன. மிங்கே மேம்பட்ட உபகரணங்கள் மட்டுமல்லாமல் தொழில்முறை வாடிக்கையாளரின் வடிவமைப்பை நனவாக்குவதற்கு அனுபவமிக்க பொறியாளர்கள், ஆபரேட்டர்கள் மற்றும் ஆய்வாளர்கள் குழு.
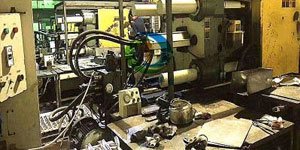
டை வார்ப்புகளின் ஒப்பந்த உற்பத்தியாளர். 0.15 பவுண்டுகளிலிருந்து குளிர் அறை அலுமினியம் டை காஸ்டிங் பாகங்கள் அடங்கும். 6 பவுண்ட்., விரைவான மாற்றம் அமைத்தல் மற்றும் எந்திரம். மதிப்பு கூட்டப்பட்ட சேவைகளில் மெருகூட்டல், அதிர்வு, நீக்குதல், ஷாட் குண்டு வெடிப்பு, ஓவியம், முலாம், பூச்சு, சட்டசபை மற்றும் கருவி ஆகியவை அடங்கும். 360, 380, 383, மற்றும் 413 போன்ற உலோகக் கலவைகள் அடங்கும்.
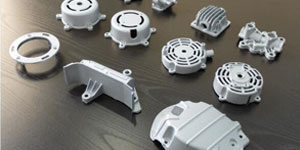
துத்தநாக டை வார்ப்பு வடிவமைப்பு உதவி / ஒரே நேரத்தில் பொறியியல் சேவைகள். துல்லியமான துத்தநாக டை வார்ப்புகளின் தனிப்பயன் உற்பத்தியாளர். மினியேச்சர் வார்ப்புகள், உயர் அழுத்த டை வார்ப்புகள், மல்டி-ஸ்லைடு அச்சு வார்ப்புகள், வழக்கமான அச்சு வார்ப்புகள், யூனிட் டை மற்றும் சுயாதீன டை வார்ப்புகள் மற்றும் குழி சீல் செய்யப்பட்ட வார்ப்புகள் தயாரிக்கப்படலாம். வார்ப்புகளை 24 இன் வரை நீளத்திலும் அகலத்திலும் தயாரிக்கலாம். +/- 0.0005 இன். சகிப்புத்தன்மை.
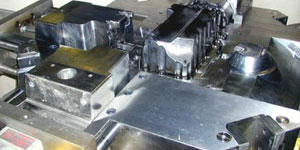
ஐஎஸ்ஓ 9001: 2015 டை காஸ்ட் மெக்னீசியம் சான்றளிக்கப்பட்ட உற்பத்தியாளர், திறன்களில் 200 டன் வரை சூடான அறை மற்றும் 3000 டன் குளிர் அறை, கருவி வடிவமைப்பு, மெருகூட்டல், மோல்டிங், எந்திரம், தூள் மற்றும் திரவ ஓவியம், சிஎம்எம் திறன்களுடன் முழு கியூஏ , அசெம்பிளி, பேக்கேஜிங் & டெலிவரி.
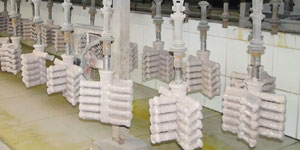
ITAF16949 சான்றிதழ். கூடுதல் வார்ப்பு சேவை அடங்கும் முதலீட்டு நடிகை,மணல் வார்ப்பு,ஈர்ப்பு வார்ப்பு, இழந்த நுரை வார்ப்பு,மையவிலக்கு வார்ப்பு,வெற்றிட வார்ப்பு,நிரந்தர அச்சு வார்ப்பு, .இடிஐ, பொறியியல் உதவி, திட மாடலிங் மற்றும் இரண்டாம் நிலை செயலாக்கம் ஆகியவை அடங்கும்.
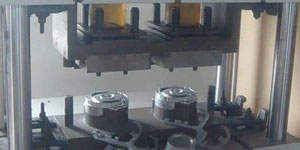
வார்ப்பு தொழில்கள் இதற்கான பாகங்கள் வழக்கு ஆய்வுகள்: கார்கள், பைக்குகள், விமானம், இசைக்கருவிகள், வாட்டர் கிராஃப்ட், ஆப்டிகல் சாதனங்கள், சென்சார்கள், மாதிரிகள், மின்னணு சாதனங்கள், இணைப்புகள், கடிகாரங்கள், இயந்திரங்கள், இயந்திரங்கள், தளபாடங்கள், நகைகள், ஜிக்ஸ், தொலைத் தொடர்பு, விளக்கு, மருத்துவ சாதனங்கள், புகைப்பட சாதனங்கள், ரோபோக்கள், சிற்பங்கள், ஒலி உபகரணங்கள், விளையாட்டு உபகரணங்கள், கருவி, பொம்மைகள் மற்றும் பல.
அடுத்து என்ன செய்ய நாங்கள் உங்களுக்கு உதவ முடியும்?
Home முகப்புப்பக்கத்திற்குச் செல்லவும் டை காஸ்டிங் சீனா
→உதிரிபாகங்கள்-நாம் செய்ததை கண்டுபிடி.
→ தொடர்புடைய உதவிக்குறிப்புகள் வார்ப்பு சேவைகள் இறக்கவும்
By மிங்கே டை காஸ்டிங் உற்பத்தியாளர் | வகைகள்: பயனுள்ள கட்டுரைகள் |பொருள் குறிச்சொற்கள்: அலுமினிய வார்ப்பு, துத்தநாக வார்ப்பு, மெக்னீசியம் வார்ப்பு, டைட்டானியம் வார்ப்பு, எஃகு வார்ப்பு, பித்தளை வார்ப்பு,வெண்கல வார்ப்பு,வீடியோவை அனுப்புதல்,நிறுவனத்தின் வரலாறு,அலுமினியம் டை காஸ்டிங் | கருத்துரைகள் ஆஃப்